Installation of Piping in Steel, Stainless Steel, and Aluminum (Global Fries)
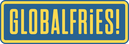
The customer
Global Fries is a producer and global exporter of fries.
Purpose
Optimise production process by modifying existing and installing new installations.
Problem-solution
Global Fries enlisted our team to provide all utilities to the machines; a combination of steel piping in schedule 40 for steam, stainless steel piping DN25 to DN250 and compressed air piping in Airnet aluminium pipe.
- The steam peeler conveyor belt was enlarged for which our team adjusted the steam supply
- For the optical grader on compressed air, we provided the supply lines for compressed air, glycol, hard and city water, among others.
- For the accept and reject flow under the optical graders, we were in charge of installing the water pipes containing starchy water (DN150 - DN250).
- To prevent mechanical components from freezing in the freezing tunnel zone, steam is sprayed or injected. We were responsible for this steam and condensate return line.
- For the packaging line, we provided the pipeline for the compressed air supply.
Thanks to the new installation, the production process was optimised:
- The line has eliminated a number of bottlenecks that allow Global Fries to produce at higher capacity.
- The overall line and utilities also became more performant and reliable, increasing production efficiency.
- Thanks to the more stable operation, the customer manages to achieve the predetermined quality more easily.
In a successful collaboration with SPARQ:
The pre-engineering was done by SPARQ and due to a previous successful collaboration for another fries processing company, we were soon on the same wavelength.
- In the engineering phase, SPARQ provided an estimate for the quantity of meters and fittings. Subsequently, we prepared a budgetary quote with indicative additional charges per meter and fitting.
- This way, the client knew roughly what to expect in terms of budget and we did not have to wait for a detailed engineering (as there was no such time).
- The flexibility of our team allowed us to respond well to the needs of the project. Based on engineering progress and production downtime, we smoothly switched the number of colleagues on site to ensure an efficient installation.
- On projects where there is not always time to do detailed engineering, the vast technical baggage of our technicians makes a decisive difference. Which always saves our client a lot of time and money. This combined with good project coordination from SPARQ ensured a successful project.
Tight planning & efficient follow-up:
- To meet the deadline, we had to use 25% of our capacity. In total, we prepared 700 metres of piping (from DN25 to DN200) in four weeks.
- In 7 days of production downtime, we were able to switch and connect everything.
- After the project, our people stayed onsite for another 4 weeks or so to take care of additional, unforeseen works.
This project represented a major challenge that we look back on with great pride. It required not only careful planning and efficient follow-up, but also shows the commitment and dedication of our entire CGK team.