Renewal of storage tanks and filling stations (Rousselot)
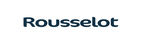
The customer
Rousselot specializes in collagen-based solutions for the health & nutrition, (bio)medical, and pharmaceutical sectors.
Purpose
The Ghent division of Rousselot called on CGK for the replacement of an outdated installation.
Problem-solution
After getting acquainted with the company, their needs, and the available infrastructure, we got to work.
At the unloading area, the truck is connected to the installation to safely pump the hazardous substances (hydrochloric acid, sodium hydroxide, sulfuric acid, hydrogen peroxide, and aluminum sulfate).
CGK was responsible for:
- The engineering of the entire project: From concept and budget determination to planning and designing the complete installation.
- The replacement of 2 outdated tanks for hydrochloric acid (HCL) and sodium hydroxide (NaOH) with 2 double-walled HDPE tanks.
- The HCL tank (70,000 liters) is equipped with an active gas scrubber that neutralizes the hydrochloric acid fumes after they exit the tank vent.
- The NaOH tank (60,000 liters) is an insulated storage tank. Since sodium hydroxide solidifies at too low a temperature, it is crucial to maintain a constant temperature. Heating elements were installed at the bottom of the tank, in a double configuration, so that if one of the elements fails, the temperature remains guaranteed.
- The installation of 5 filling stations with controls, 2 for the brand-new tanks and 3 for the existing tanks.
- Each filling station is equipped with pressure measurement, flow rate frequency control, and the filling valve automatically closes in case of problems.
- Because HCL is highly corrosive, the filling station for hydrochloric acid was equipped with a pump to safely transfer the liquid.
- The entire installation complies with VLAREM regulations. Each tank is equipped with:
- An overfill protection at the top.
- Leak detection in the jacket.
- A signal box that triggers an alarm in case of issues.
- Ultrasonic measurement, allowing for accurate real-time monitoring of the liquid percentage in the tank. As a backup, a level float system is also in place, so the liquid level can be monitored even in the case of an electrical failure.
- The assembly and insulation of the piping from the filling stations to the storage tanks.
The team that realised this project
Project Engineer Tim
Technical Designer Nick
Fitter Jo
Fitter Sander
Fitter Jonathan
Fitter Sebastien
Fitter Thibaut